プラスチック部品ができるまで
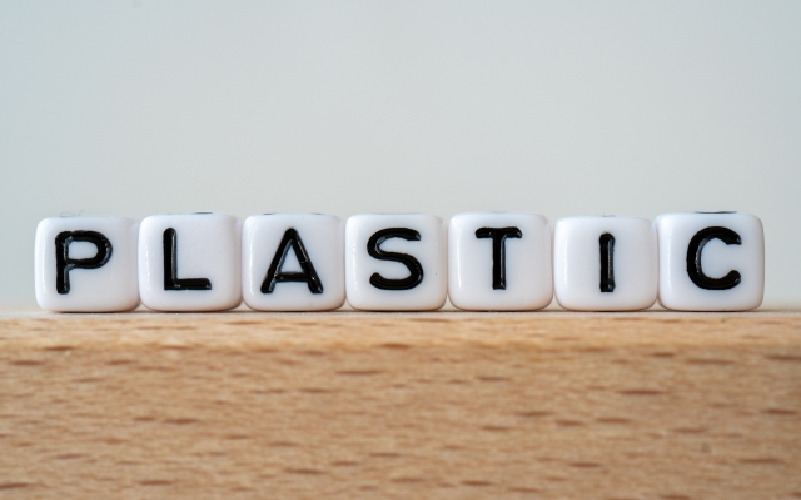
射出成形とは?
■プラスチック部品ができるまで
プラスチック部品は射出成形という方法で作るのが一般的です。
射出成形とはプラスチック樹脂を溶かして金型に射出することで成形する手法です。
射出成形で準備するものは材料、金型、射出成形機の3つで、それぞれについて説明します。
■材料
プラスチック部品はペレットと呼ばれる粒状の樹脂(合成樹脂)から作られます。
射出成形では熱によってペレットを固体から液状に融解させます。
液状になった樹脂を冷やすことで再び固体に変化させ、形を作ることができます。
■金型(A案)
熱によって融解した樹脂を成形するためには、流し込むための金型が必要です。
金型は名前の通り、金属でできた型であり、一般的には「タイ焼き機」がそれにあたりま
す。
射出成形に用いる金型は、製品の品質に直結するので非常に高い精度が求められます。
高品質の金型を使うことで、同じ形の製品を大量かつ、高い精度で作ることが可能です。
弊社協力会社は金型の設計から製作、それを用いた量産にまで対応しています。
そのため、急な設計変更依頼などにも迅速に対応が可能です。
■射出成形機(ボリューム追加案)
先ほどの金型を射出成形機にセットして射出成形が始まります。
射出成形は大きく分けて8工程あります。
射出成形機内部で何が行われているのかを詳しく説明していきます。
1 材料の準備
ホッパーといわれる投入口に材料を投入します。(投入前にペレットの材質によっては乾燥工程が入ります。)
その後シリンダー内でヒーターを用いて樹脂を融解させ、射出に備えます。
2 型締め
金型に、融解させた樹脂を射出する前に、2つに分かれている金型を適切な力で締めます。
3 射出
溶かした樹脂を射出させ、金型内に充填させます。
射出する際には、適切な速度での射出でないと不良品ができてしまうため、速度の設定が重要です。
4 保圧
融解した樹脂に圧力をかけて形を安定させます。
5 冷却
融解した樹脂を、金型内で冷やし固めます。
冷却時間が短いと取り出す際に製品が変形してしまい、長すぎると金型にくっついて取り出
す際に傷が残ってしまうことがあるため、適切な冷却時間を知ることが重要です。
6 計量
冷却している時間を利用し、次の射出成形に必要な樹脂を計量して溶かしておきます。
7 型開き
冷却し、固化した成形品を取り出すために型を開きます。
8 製品取り出し
エジェクターで成形品を押し出して、取り出し機で取り出します。
今回はプラスチック部品を作るための射出成形についてご説明しました。
工程自体はシンプルなものですが、金型は精度によって大きくコストが変わるため、入念な打
ち合わせが必要となります。
私たちは、金型の設計製作から、成形、組み立て、検査、梱包、出荷までの流れを一貫で対応
することで、品質・コスト・納期に対応してまいります。
医療用部品やコネクタなど、高信頼性や特殊なノウハウが要求される製品もお任せください。
費用が知りたい、こんな製品は作れるかなどのご相談はジェスコまでお問い合わせください。